In an ideal world, a pull system would be the best mechanism for replenishing inventory in distribution centers. But those unplanned and often unexpected pulls can cause chaos in the supply chain.
CrescentOne DRP
With the new GLOVIA G2 ERP software module, Distribution Requirements Planning, a user can have the best of both worlds, a Kanban or pull system for replenishment purposes, backed up with planning for the likely supplies needed.
From the Distribution Center (DC) perspective, whether there are multiple remote locations or simply a location at the plant, a pull mechanism is the most efficient for replenishment. There may be space constraints that limit the amount of inventory that can be carried and excess inventory may cause problems. Putting to one side the additional carrying costs of that inventory, GLOVIA G2’s Distribution Requirements Planning software module allows companies to plan the correct levels of inventory at those locations and automate the replenishment process, thus reducing costs and creating efficiencies at the distribution level.
The inputs to this calculation start with a forecast as to the likely consumption of an item over time. Forecasts tend to be relatively “flat”, so along with the forecast the GLOVIA G2 Distribution Requirements Planning software module looks at shipment history to calculate the likely standard deviation, and therefore coefficient of variation, and apply that to the likely demand. Other factors taken into account are the transport lead time from the supply source to the DC, the manufacturing lead time and the manufacturing cycle. The manufacturing cycle tells the system how often a particular item should run. It may be possible to manufacture a batch every day, but efficiencies dictate that a particular item will be manufactured only once every week. Of critical importance is the service level a company wants to provide, which is an additional input that needs to be factored into the planning process. Based on all the inputs, the system will calculate a time-phased plan for each DC where re-order point and re-order quantity (ROP & ROQ) vary over time. Time periods are user defined and are typically weeks, months or quarters, depending on market volatility.
The longer a time period, the more likely it is that the quantity difference between any two periods may be significant and the supply chain may be challenged to supply the difference, or it may be hard to slow down supplies quickly at the end of a period. Recognizing this, the GLOVIA G2 Distribution Requirements Planning software system allows a user to define “ramp” duration at each end of a period where quantities may be ramped up or down to reach the period levels more efficiently.
Inventory Forecast Simulation
Users have multiple simulations available to be able to plan future periods. For example, a business can create a DRP plan for future periods, test this plan against their manufacturing or supply capability and make adjustments where necessary. Once a workable and agreed upon plan is reached the simulation is copied into the current plan.
With the ROP and ROQ set for a period and the ramp durations set if necessary, the system is now ready to automatically generate supply orders when inventory falls below the ROP
If the DCs are remote from the manufacturing plants these supply orders take the form of GLOVIA G2 Transfer Orders. The Transfer Orders can be used as part of the planning cycle in the plant, or the system can automatically generate the manufacturing orders or purchase orders needed to supply the Transfer Orders, shortening the planning cycles further.
However, if the manufacturing plant has no visibility of the Transfer Order until it is generated, the plant may have a hard time responding to the new demand from a material or capacity perspective, and transport planners will have no visibility as to transportation requirements.
To mitigate these problems, GLOVIA G2 now takes the ROP and ROQ into account in Master Production Scheduling and Material Requirements Planning. During planning, based on known demands, inventory, and supplies in transit for the DC, our planning engines will predict when a ROP will be triggered and generate new Computer Planned Transfer Orders (CPTO).
At the manufacturing plant these CPTOs can be used to generate a procurement plan and a capacity or skill plan to be able to meet the likely demands when order shipments arrive. These CPTOs will also be used to plan transportation requirements.
At this stage a business will have created a Sales and Operations plan in support of the customer service activities that will minimize inventory and maximize efficiencies. Planners throughout the distribution requirements planning system have the visibility they need to plan, but execution is still done on a pull system.
This combination of planning and a Kanban, or pull system, will yield greater efficiencies and improved processes for your Distribution Requirements Planning.
Download CrescentOne data sheet for more information about GLOVIA G2 Distribution Requirements Planning (DRP) ERP software.
DownloadExplore More Capabilities
Select a product category below to see how CrescentOne can improve a particular aspect of your business
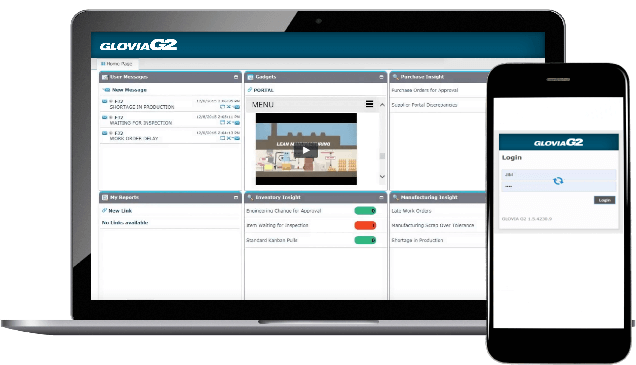