Flexibility
The Work Orders management module gives you the flexibility you need to effectively manage any type of manufacturing, assembly, repair, or work activity. Whether you are manufacturing products based on forecasts, demands or Kanban signals, or building engineering prototypes, managing an entire development project or conducting repair work –this production management system offers a single familiar tool that your whole team can use to schedule, manage and collect data for all work activities.
The flexible multiple line architecture of the Work Orders management module provides the ability to manage many different business scenarios including:
- Scheduling multiple production runs of a single item on a single work order,
- Creating multiple orders, lines or ‘splits’ for a single item, (even when they need to have the exact same date and time).
- Providing multiple items and/or services for a specific ‘job’ – all on a single work order
- Controlling the multiple phases of ‘prototype to production’ activities on a single work order – with each phase identified as a separate distinct line on that order.
Scheduling Accuracy
Each line on a work order may identify multiple work activity dates and times. These can be automatically determined using the GLOVIA G2 scheduling and optimization capabilities. Schedules are defined to the specific hour, minute and second.
Back-flush Operations
Optimal production operations often require discrete as well as repetitive manufacturing styles. This production management system delivers the best of both worlds by allowing users to simultaneously support a hybrid-manufacturing environment. The Work Orders management module’s back-flushing capabilities include:
- Back-flushing of materials/components at a specific operation, as a quantity is completed, or as assembly or operation scrap is recorded
- Back-flushing from both centralized (floor-stock) and line-side inventory locations
- Back-flushing of fully lot controlled and serial controlled items.
Multi-Level Material Pegging
Material Requirements Planning processing logic honors full level material pegging generated by GLOVIA G2 Project Resource Planning (PRP). This ensures that your free stock, commitments, and netting calculations display the pegging of replenishment orders to provide complete hierarchical material visibility at all levels.
Outside Processing and Subcontracting Manufacturing and/or Processes
This production management system enables you to quickly and simply generate purchase orders for any outside processes that need to be conducted
Advanced outside process management capabilities (Material Supply) provide for the planning, provisioning and tracking of supplied/consigned materials that you need to ship to your supplier in order the subcontracted manufacture or manufacturing process to be completed and received on time. The subsequent manufacturing or shipping activities can then be immediately invoked, as the receipt from the supplier is automatically directed to the next stage in the process.
Complete Integration
The Work Orders management module is an integral part of the GLOVIA G2 integrated ERP, Financial and Supply Chain solution that resides on a single database.
When a user records the completion of a manufactured quantity, they are instantly advised if the necessary mandatory quality processes and measurements have not yet been recorded.
Where lot/serial traceability is critical – exceptions will immediately identify any component issues where traceability was not recorded.
Substitutes, Alternates, Bills of Materials and Routings
For each line item on a work order, the production management system provides the option to identify a unique bill of material (BOM) and routing for that line.
This provides the ability to:
- Select an alternate BOM, or component substitutes
- Select an alternate routing or create a ‘tailored’ production routing, or
- Even create a completely unique custom BOM and routing configuration.
This flexibility is critical when trying to manage production around customer specifications, limited material availability and capacity, resource, skill and/or tooling constraints.
The production management system’s unique order-specific BOM and routing records also provide the basis for order tracking, cost auditing, and the as-built product configuration control documentation.
Multiple Costing Methods
When dealing with a range of products or projects, you need a flexible cost collection solution that supports multiple costing methods. This production management system ensures flexibility, with the ability to select the cost methods most appropriate to the job at hand.
Visibility of standard, average and actual costing variances is provided.
By providing for the separate identification of both cost centers and a work centers – routings can accurately support the needs of both cost accounting and resource/capacity planning without having to compromise.
Work-in-Process Visibility
You always have instant and accurate visibility to your current investments in work-in-process inventory. Each work order provides an online valuation of the materials used and value-added costs. The total value of completed items is tracked for easy comparison to the planned work order costs and accumulated detail costs. Labor and machine efficiency data is generated and all transaction activity is tracked and calculated for financial posting and reporting.
Other key capabilities:
- Integration with Engineering
- Change Module
- Trial-kitting
- Multi-order committing based on priorities
- Lot and serial control and traceability
- Pick-lists, Pull-tickets, direct issues, issue on receipt or completion
- Shop packetsProduction dispatch lists and insights drive production activity.
- Labor and machine times and rates
- Outside processing activity and costs
- Scrap transactions for assembly, component, and operation
- Completion tolerances control completed quantity over/under
- Manufacturing close prevents further manufacturing activity
- Financial close identifies and creates GL entries for cost variances.
- Manufacturing and financial closes are reversible
Download CrescentOne data sheet to learn more about GLOVIA G2’s Work Orders production management system.
DownloadExplore More Capabilities
Select a product category below to see how CrescentOne can improve a particular aspect of your business
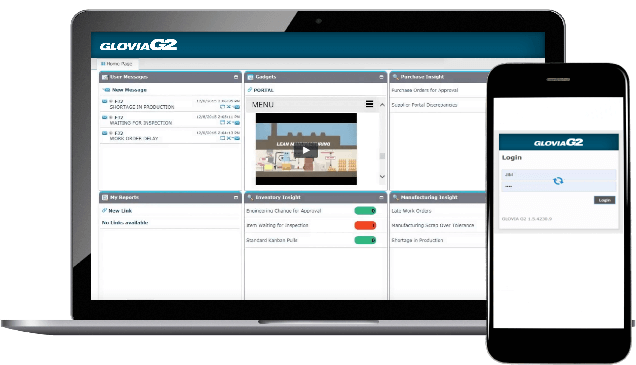